Coated paper suppliers
At XiangGe Package, we specialize in high-quality single-side coated paperboard that delivers exceptional results across diverse industries. Our premium packaging solutions are trusted by leading brands in: food, beverage, electronics, beauty, fashion, e-commerce & shipping.
Contact XiangGe Package today – let’s create packaging that sells your products and tells your story.
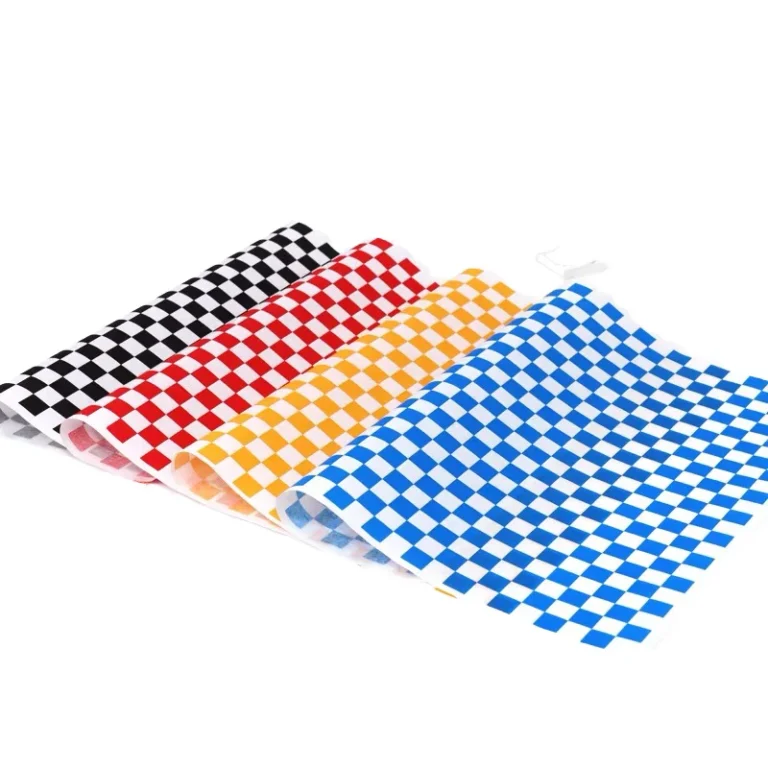
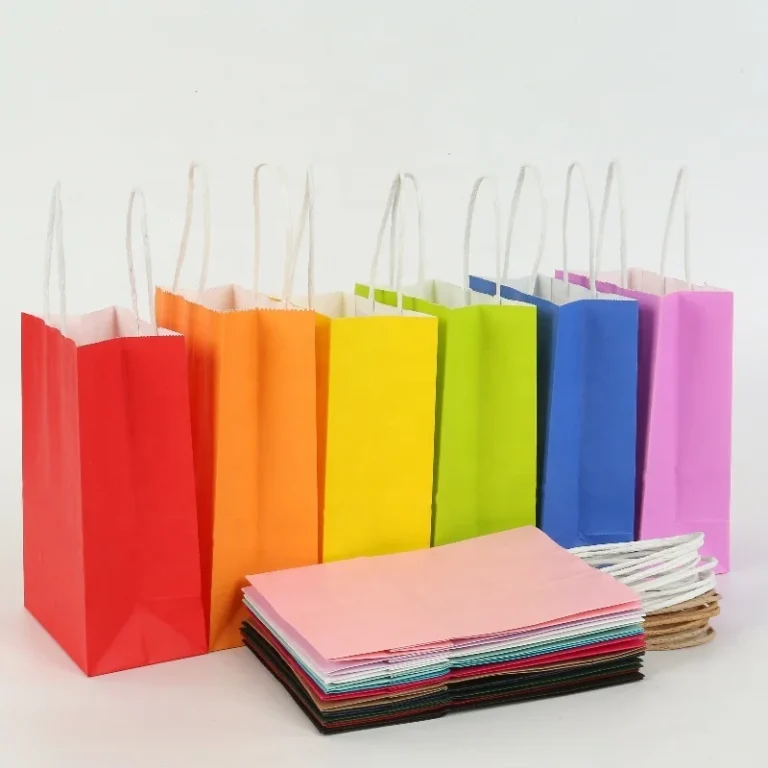
Common basis weight specifications:
- Lightweight coated paper: 60, 70, 80g/m ².
- Standard coated paper: 100, 110, 128g/m ².
- Heavy duty coated paper: 157, 180, 200, 220, 250, 280, 300g/m ².
- Overweight coated paper: 330, 350, 400g/m ².
- Specification
- Overview
- Relative Information
- FAQs
3 Main Types of Coated Cardboard:
Coated Linerboard
- Primary use: Face material for corrugated boxes and rigid fiberboard.
Coated Duplex Board
- Primary use: Single-sided color printing applications.
Coated White Cardboard
- Primary use: Premium packaging applications.
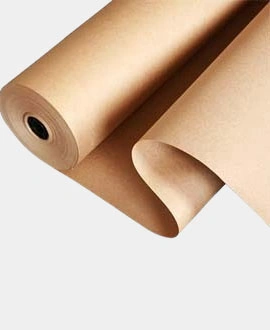
Coated Linerboard
Brightness ≥ 80-98%
Glossiness ≥ 40-70 Glossiness units
Printing surface roughness ≤ 3.5 μ m
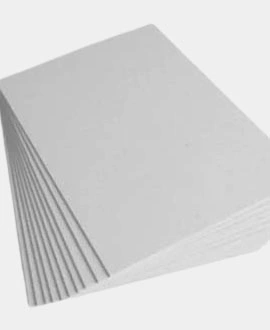
Coated Duplex Board
Weight: 200-400 g/m ²
Thickness: above 0.1mm
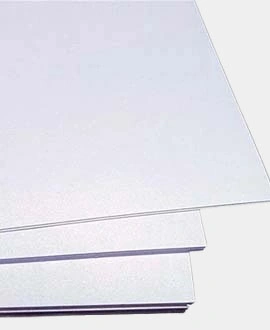
SBS
C1S: Single powder card, coated on one side
C2S: Double powder card, double-sided coating
Functional coated paper types
Coated paper can be divided into the following 4 types according to their functions:
- Waterproof
- Oil
- PE
- Barrier
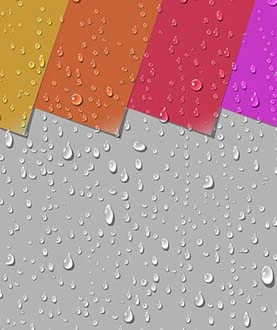
Waterproof
Up to the highest waterproof standard of R10.
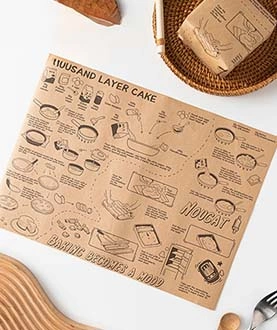
Oil resistance
Prevent oil penetration and protect food and industrial products.
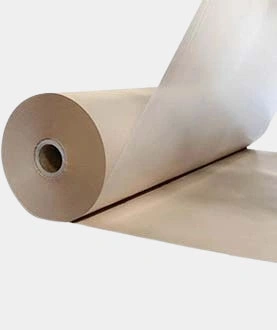
PE
Moisture proof, waterproof, oil proof, and have good air tightness.
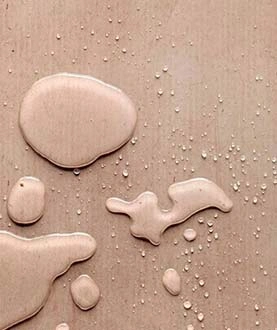
Barrier
Block water vapor, oxygen, fragrance, etc
Printing purpose
Divided into 3 categories based on glossiness.
- Glossy
- Matte
- Semi-gloss
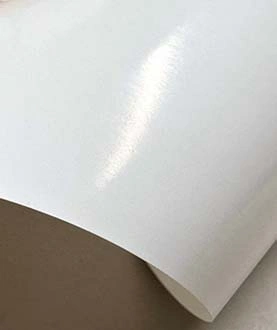
Glossy
High gloss, good mirror reflection effect
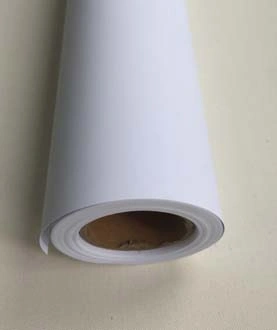
Matte
Matte, with a soft texture
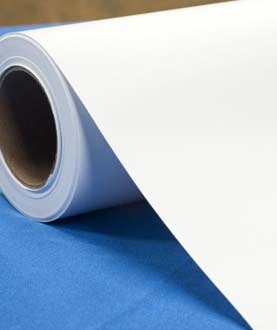
Semi-gloss
Balancing visual effects and practicality between smooth and matte surfaces.
Food packaging coated paper
It can be roughly divided into three categories:
- Food grade
- Heat-resistant
- Frozen food

Food grade
The packaging that comes into direct contact with food complies with FDA and GB standards.
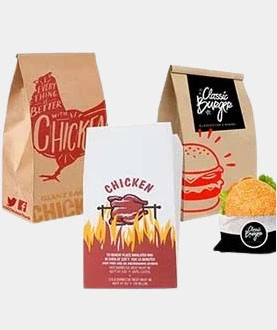
Heat-resistant
Can withstand high temperatures of 80-120 ℃, suitable for hot drinks and food.
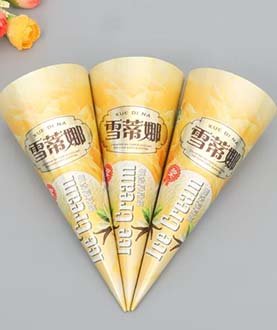
Ice Cream Coated Paper
Maintain stable performance at -18 ℃ to prevent the influence of condensation water.
What is coated paper
Coated paper is regular paper that has been treated with a special coating on one or both sides. Think of it like putting a smooth, glossy layer on top of regular paper – similar to how you might apply a protective coating to wood furniture.
The coating is typically made from materials like clay, calcium carbonate, or other minerals mixed with binding agents. This coating fills in the tiny gaps and rough spots on the paper’s surface, creating a much smoother, more uniform printing surface. Learn many package boxes materials types.
- Smoother surface than regular uncoated paper
- Better ink absorption control – ink sits on top rather than soaking in
- Enhanced print quality with sharper images and text
- Available in different finishes – glossy, semi-gloss, or matte
- Various weights from lightweight (80gsm) to heavy cardstock (400gsm+)
Coated vs uncoated paper plates
Comparison Item | Coated Paperboard | Uncoated Paperboard |
---|---|---|
Surface Smoothness | Excellent (50-70 gloss units) | Average (10-30 gloss units) |
Printing Quality | Excellent, bright saturated colors | Average, easy ink penetration |
Water Resistance | Good, has barrier properties | Poor, easily absorbs moisture |
Wear Resistance | Good, coating protection | Average, surface easily worn |
Writability | Poor, ink hard to stick | Excellent, easy to write on |
Production Cost | High (15-25% more cost) | Low (basic production cost) |
Market Price | 20-40% higher than uncoated | Base price |
Premium Product Price | 50-60% higher than uncoated | Base price |
Recyclability | Recyclable 5-7 times, complex process | Simple recycling, less loss |
Eco-processing Difficulty | Needs de-inking, higher energy use | Simple processing, low energy |
Biodegradability | Coating slows decomposition | Fully biodegradable |
Production Environmental Impact | Chemical coating emission risk | Minimal environmental impact |
Complete performance comparison table of both papers.
Manufacturing Cost Differences
Coated Paperboard: Higher production cost
- Coating process adds 15-25% to production cost
- Needs special coating equipment and precise control systems
- Coating materials (clay, calcium carbonate) increase material costs
Uncoated Paperboard: Lower cost
- Simple production process, no coating equipment needed
- Lower raw material costs (mainly pulp and basic chemicals)
- Higher production efficiency and output
Recycling Comparison
Coated Paperboard:
- Can be recycled 5-7 times
- Eco-friendly coated paperboard is “recyclable and can be repulped for reuse“
- Coating makes recycling process more complex and increases de-inking difficulty
Uncoated Paperboard:
- Simpler recycling process (no coating removal needed)
- Higher recycling rate with less fiber loss
- Less environmental pollution
Although coated paperboard costs more and has complex environmental impacts, its advantages in printing quality, functional performance, and brand value make it the mainstream choice in modern packaging industry. With environmental technology progress and cost optimization, coated paperboard will continue strong market growth.
Yes, the surface has a thin layer of polyethylene plastic. During recycling, this plastic layer can be removed and separated. Since the main part is paper, recycling is very important. It helps reduce waste in landfills and saves natural resources.
Coated paper is made from wood pulp fibers, calcium carbonate, and synthetic latex. These materials are safe and have stable properties. The coating layer is also non-toxic and has no smell. Our coated paper meets all environmental and safety standards.
Coated paper is also called art paper or glossy paper. It is made by adding a white coating to the paper surface. This makes the surface smooth and shiny, which is perfect for high-quality printing.
Coated paper does not absorb ink well and may get stained, especially with too much ink or rough handling. Compared to specialty papers, it is softer and less rigid.
There are several ways to check if paper has a coating:
- Look at the surface - Check if it looks smooth and shiny.
- Touch test - Feel if the surface is smooth.
- Water test - Put a small drop of water on the surface to see if it soaks in.
- Equipment test - Use ultrasonic or other tools to measure coating thickness and density.
Wholesale coated paper boxes
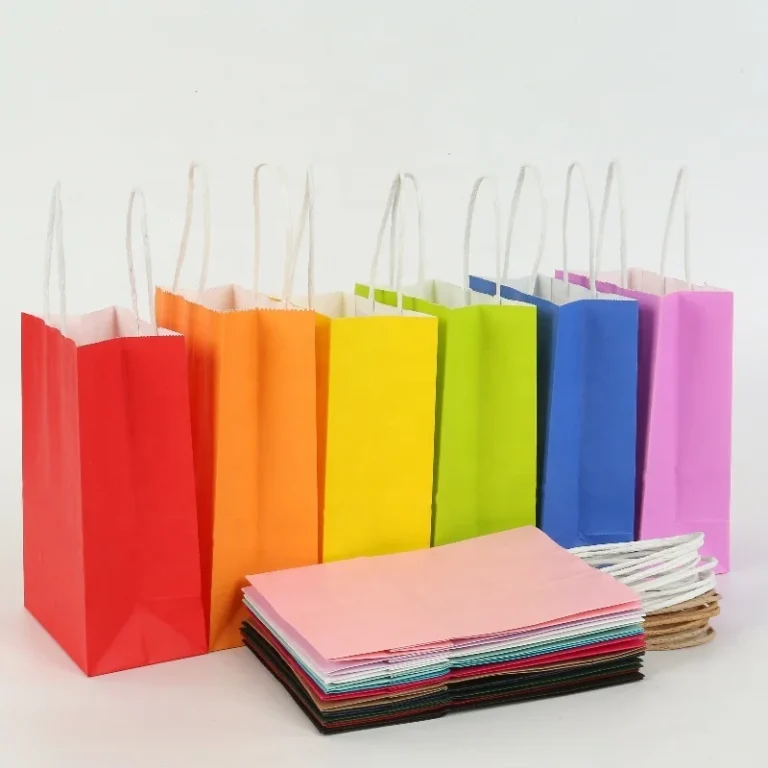
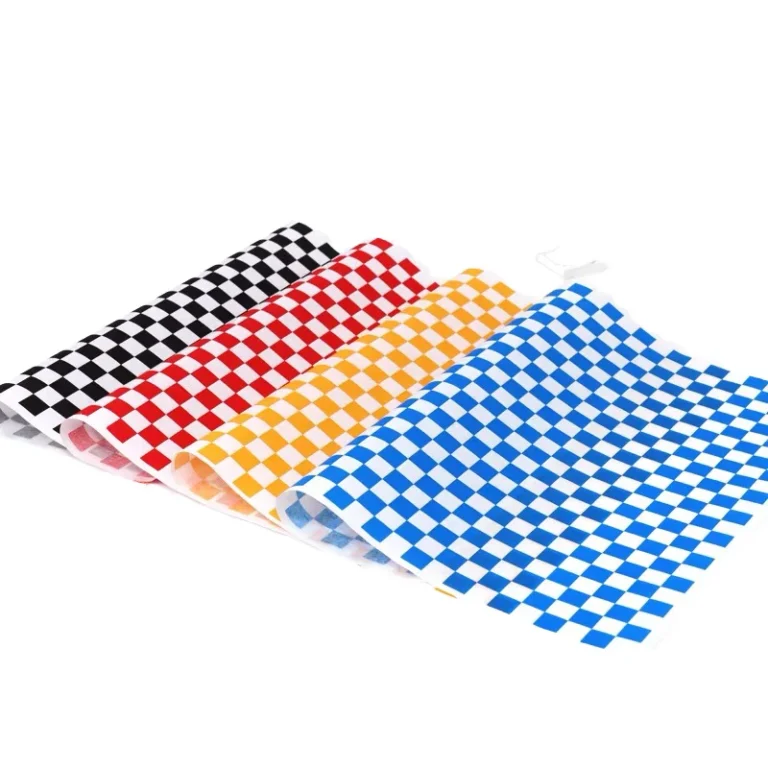
The advantages of high-quality coated paper
High-quality coated paper gives clear benefits that improve both print quality and business efficiency. Research in printing technology strongly supports these advantages.
A 2020 study in Cellulose Chemistry and Technology journal showed that high-quality coated paper provides excellent color accuracy and print density control.
- Better ink efficiency: High-quality coated paper needs only 0.752 g/m² of ink to reach the ideal density of 1.40, meeting ISO 12647-2 color standards.
Superior surface quality: Test results show excellent properties – 99% brightness, 94% opacity, and 70% gloss – which directly improve print quality.
Reliable color matching: The smooth, uniform surface gives more predictable and accurate colors.
How XiangGe Package produce coated paper boxes
Below are our box package manufacturing process:
- Material preparation: We use coated paper for the surface and corrugated paper for the inner layer.
- Printing: We choose the right printing method based on the design and requirements. We add anti-offset powder to prevent ink from sticking.
- Surface treatment: If needed, we add film coating, wax coating, calendering, embossing, or hot stamping to improve the appearance.
- Die cutting and creasing: We make cutting plates based on the box design. Then we cut and crease the paper to create fold lines and slots for easy assembly.
Assembly: We use the fold lines to shape the box through gluing, stapling, or stitching.
Quality check and packaging: We inspect the finished boxes for size, print quality, and strength. Then we arrange shipping by sea or express delivery.
Why choose us as coated paper manufacturer
Choosing us for your copperplate paper and cardboard boxes will make your product packaging look better and help you stand out in the market.
High quality
Your coated paper boxes deliver excellent print quality and visual appeal, boosting your product packaging and brand image while strengthening market position.
Edge tech
Our coated paper uses high-quality coating technology for a smooth, fine surface that creates bright, clear printing and enhances packaging appearance.
Customization
We offer custom printing, surface treatments, and box designs to meet both functional and visual needs for different products.
Durable
By combining coated paper's excellent printing with corrugated paper's strength, our boxes provide good compression resistance and protection during shipping.
Fully solution
We provide complete packaging solutions from material selection and design to production and quality control, with delivery in 10-15 days.